A well-designed edge trim system will help ensure that your production machine can run at its best without stops due to edge trim breaks or full trim bins that need to be cleared.
Lundberg Tech has been designing edge trim systems for more than three decades and our team has experience in handling all types of trims – anywhere from ultrathin plastic trims to heavier cardboard trims.
When designing a trim system, we always start with an overview of the type(s) of machines, number of trims, machine speeds, factory layout and the desired destination of the trims.
Trim cutting is essential!
In our opinion cutting the trim is essential for maximum trim handling efficiency. With our high-speed trim cutters, we can cut edge trim up to a whooping speed of 2,500 m/min. When the trim is chopped into small pieces, we can easily transport the cut trim pieces over long distances, which means that the size of your plant is not a limitation in terms of bringing the trims to a collection point anywhere in your facility.
Vacuum based transport saves energy
Cutting the trim also allows us to use vacuum for transporting the chopped trim pieces, this is more efficient than using a trim blower for pushing the trim waste from the machine to the bin. Typically, a vacuum based trim system uses 3-5 times less energy than a Venturi injection-based system. At the same time using vacuum for transport of the trims allow us to place the ventilator away from the production area, hence reducing noise levels and freeing up space on the production floor.
Chopped trim compacts better
When edge trim is cut into smaller pieces it drastically reduces the volume of the waste, uncut edge trim tends to curl up in a big pile – with lots of air between the strings of trim. Confetti size trim pieces will have a higher probability of compacting by itself – and if compacted mechanically in a TrimCompactor or in a stationary compactor it can reduce the volume even more. Compacted trim means a higher density of the trims when transporting for recycling or incineration – reducing the CO2 impact from the transport.
A Lundberg Tech Trim capturing system consists of six important steps
1) Trim Capturing: A dedicated pipe for capturing the trim right where it is generated
2) Trim Cutting: A high-speed trim chopper for cutting the waste into small confetti size pieces
3) Vacuum Conveying: Transport the trim in a dedicated pipe system using one central ventilator positioned aways from the production floor
4) Trim Collection: When the trim reaches its final destination the edge trim and transport air is divided using a separator
5) Trim Compaction: Once the cut trim is collected it needs to be compacted, for easy storage transport
6) Air cleaning: The transport air used in the system should be cleaned using a manual or automatic filter, so that the air can be returned to the production area and help reduce underpressure and save energy used on cooling or heating the facility
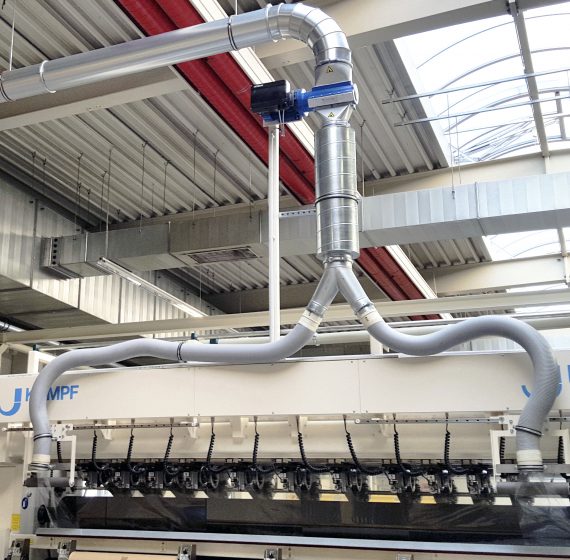
Typical edge trim processes
Lundberg Tech trim handling systems are used in a wide variety of processes.
Label printing: Glassine / release line trims created during the printing or converting process.
Slitting of film and foil: When converting larger rolls of flexible packaging edge trim is typically generated at high speed during the slitting and rewinding process.
Slitting of adhesive raw materials: When converting larger rolls of self-adhesive material a trim is often generated, with the oil system and non-stick coating on our trim cutters it is no problem to handle adhesive materials
Production of non-woven materials: Nonwoven edge trims can be hard to handle due to the thin fibers in the material, but with our UT trim cutter we can cut materials below 20 micron
Paper production: When converting paper rolls into sheets paper trims are typically created at very high speed, which demands a well-designed trim handling system – as stopping easily is not an option at 2.500 m/min!
Film extrusion: During blow film extrusion several trims are typically generated and need to be transported away in a easy and efficient way to ensure that the trims are not disturbing the extrusion process
With more than 10,000 of our trim cutters installed worldwide, we are daily helping companies cutting millions of kilometres of endless trim and thereby ensuring a smooth production.